Metodo dei cartellini rossi: che cos’è e a che cosa serve?
Da Editorial Staff
Dicembre 20, 2020
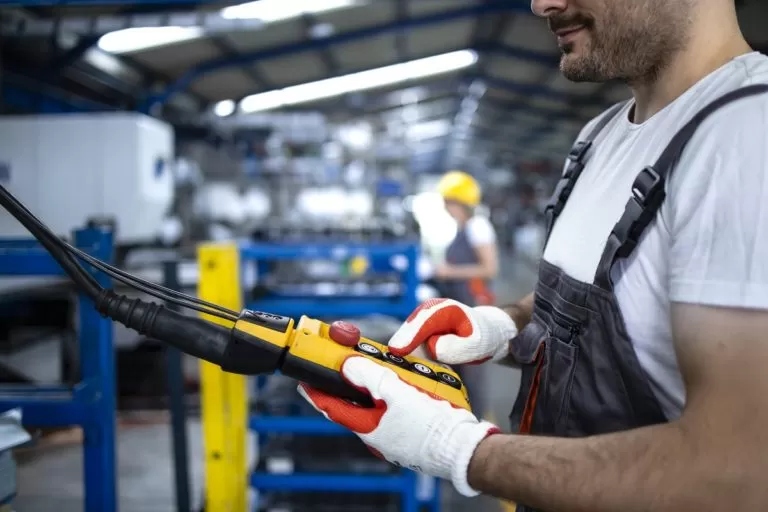
La realtà della produzione snella e della lean production è diventata sempre più diffusa all’interno della filosofia aziendale e societaria di numerosi enti che operano all’interno di diversi settori e territori. La tradizione, ereditata dalla cultura giapponese e che si struttura sulla stessa, è diventata diffusa anche all’interno della realtà lavorativa ed economica occidentale, in virtù di una traslazione continua che ha portato i processi aziendali ad adeguarsi a norme e strutturazioni differenti.
Tra questi, è degno di sottolineatura il cosiddetto metodo dei cartellini rossi, utilizzato in termini aziendali, e che risulta essere particolarmente emblematico per le sue caratteristiche. Attraverso questo metodo, in effetti, è possibile concretizzare una delle fasi fondamentali del metodo delle 5S, particolarmente utilizzato per concretizzare la lean manufacturing: la fase del seiton, che consiste nel riordinare i propri oggetti e strumenti dopo averli opportunamente separati attraverso una procedura iniziale. Ecco tutto ciò che c’è da sapere a proposito di questo metodo dei cartellini rossi, comprendendo soprattutto il suo funzionamento e la sua utilità in termini prettamente pratici.
Come funziona il metodo dei cartellini rossi?
Al fine di comprendere come avvenga il metodo dei cartellini rossi, che risulta essere parte fondante del processo di occidentalizzazione della metodologia delle 5S giapponese, è opportuno considerare le applicazioni pratiche che si ritrovano all’interno del contesto aziendale, e che si strutturano sulla base di una metodologia processuale molto semplice, e degna di una certa semplificazione della cultura giapponese del riordinare e del separare gli oggetti prima di eliminare quelli inutili.
L’approccio in questione prevede di utilizzare i cartellini rossi per segnare tutti gli attrezzi, i materiali e gli strumenti che possono risultare inutili all’interno del contesto aziendale. Ovviamente, per identificare ciò che è inutile, è opportuno operare una classificazione globale di tutto ciò che fa parte di un’azienda o di un ufficio. Una volta effettuata questa prima pratica di distinzione, basterà indicare in un’area specifica, definita di non utilizzo 8e che può essere rappresentata, anche simbolicamente, da una stanza o da un altro luogo chiuso), ciò che effettivamente è inutile per i propri processi aziendali immediati.
Se i materiali segregati in un’area di non utilizzo vengono reclamati da una persona, questa stessa dovrà offrire motivazioni valide per le quali sta reclamando un determinato oggetto; nel caso in cui queste motivazioni stesse siano effettivamente riconosciute, l’oggetto sarà identificato chiaramente come valido, e il cartellino rosso eliminato. Nel caso in cui le motivazioni non siano di stretta necessità, l’oggetto in questione manterrà il suo cartellino e non potrà essere utilizzato. Tutti i materiali che manterranno il loro cartellino, dopo un arco temporale che va dai 3 ai 6 mesi, dovranno essere eliminati, in modo da operare la fase di eliminazione della componentistica inutile all’interno di un’azienda.
I vantaggi del metodo dei cartellini rossi
Ci si potrebbe giustamente chiedere quale sia l’effettiva utilità del metodo dei cartellini rossi, soprattutto in termini di produzione smart e ottimizzazione delle risorse aziendali. Allo stesso tempo, sono diverse le perplessità nei confronti di una metodologia che, più che avere applicazioni, prevede di servirsi di una certa filosofia.
In effetti, il metodo in questione risulta essere molto prolungato nel tempo, a differenza di altre applicazioni pratiche della lean manufacturing e, per certi versi, anche lento nelle sue definizioni fondamentali. Allo stesso tempo, però, permette di ridurre al minimo i rischi di un’eliminazione troppo rapida e repentina di materiali che, in realtà, potrebbero rivelarsi utili, per quanto al momento della selezione non siano considerati come tali; in questo modo, la pulizia che avviene dopo l’arco temporale considerato sarà snella ma efficace, e porterà a un meccanismo di miglioramento continuo che determina un vantaggio considera interni aziendali.
Articolo precedente
Take Away: che cos’è, come funziona e vale la pena investirci?
Articolo successivo
TaoTrade: recensione del broker, vantaggi e opinioni
Editorial Staff
Articoli correlati
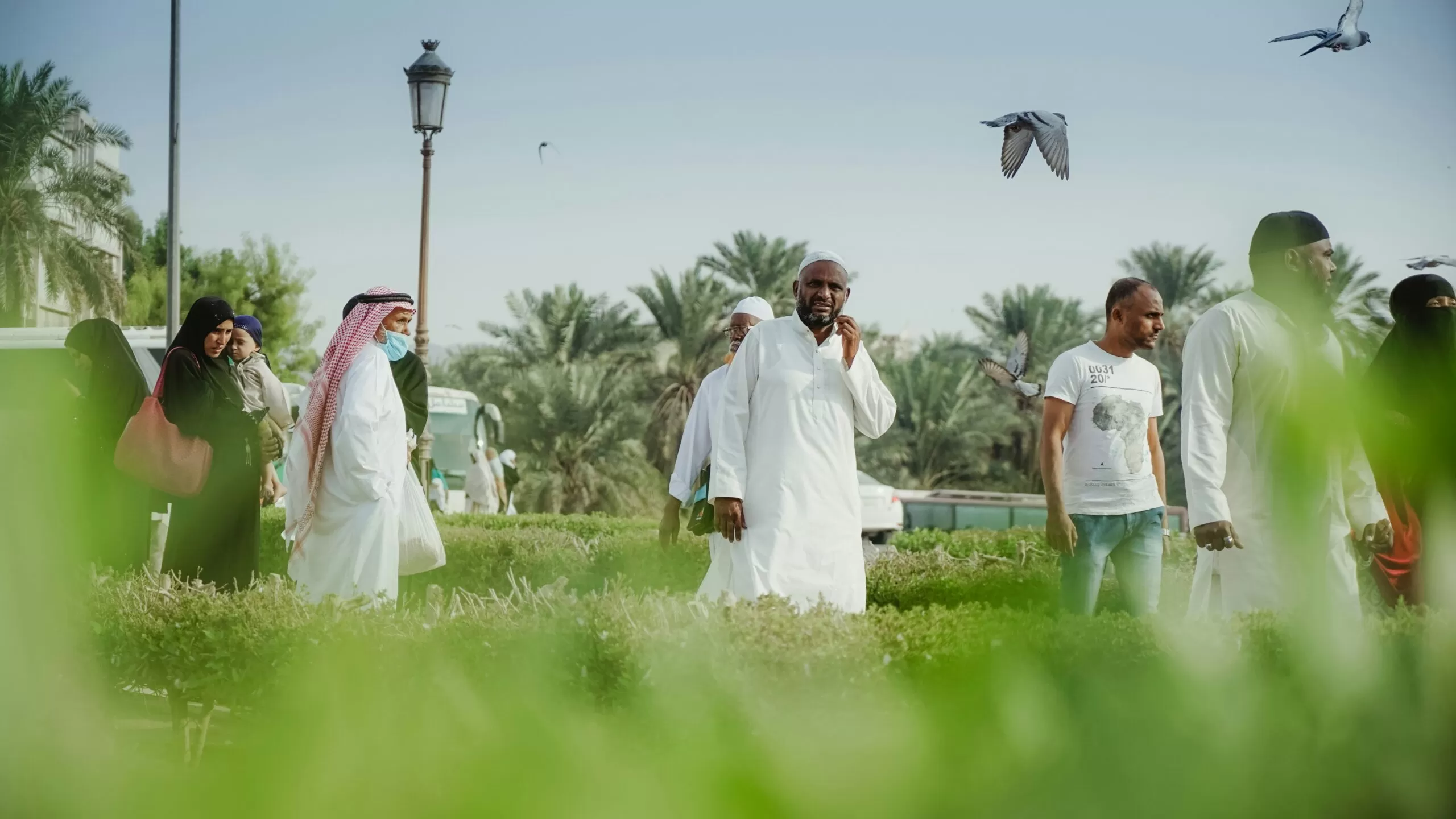
Arabia Saudita: un’economia in continua crescita
Novembre 22, 2024